Book Appointment Now
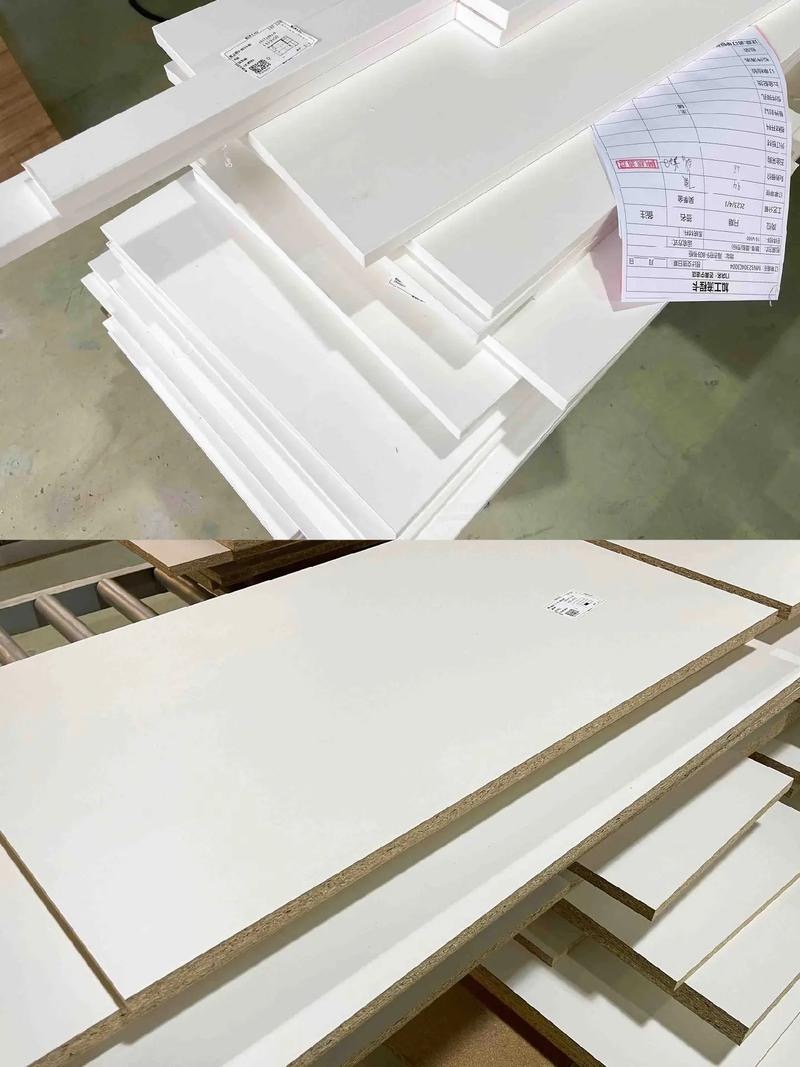
5 Common Packaging Challenges in Modular Cabinet Manufacturing—How to Solve Them
Struggling with modular cabinet packaging? Discover five common challenges manufacturers face and how smart packaging solutions can improve efficiency and reduce costs.
Packaging in modular cabinet manufacturing is far more complex than in traditional industries. With custom-sized panels, varying orders, and delicate surfaces, manufacturers often struggle with high costs, inefficiencies, and product damage.
This article explores the five most common packaging challenges in the industry and introduces smart, on-demand packaging solutions that help businesses optimize costs, improve product protection, and streamline operations.
1. Inconsistent Packaging Due to Varying Panel Sizes
The Challenge
Each modular cabinet order consists of panels with different dimensions, making it nearly impossible to use standardized pre-made cartons. This results in:
• Overly large boxes that waste materials
• Manual adjustments that slow down production
• Increased risk of damage during transit due to improper fits
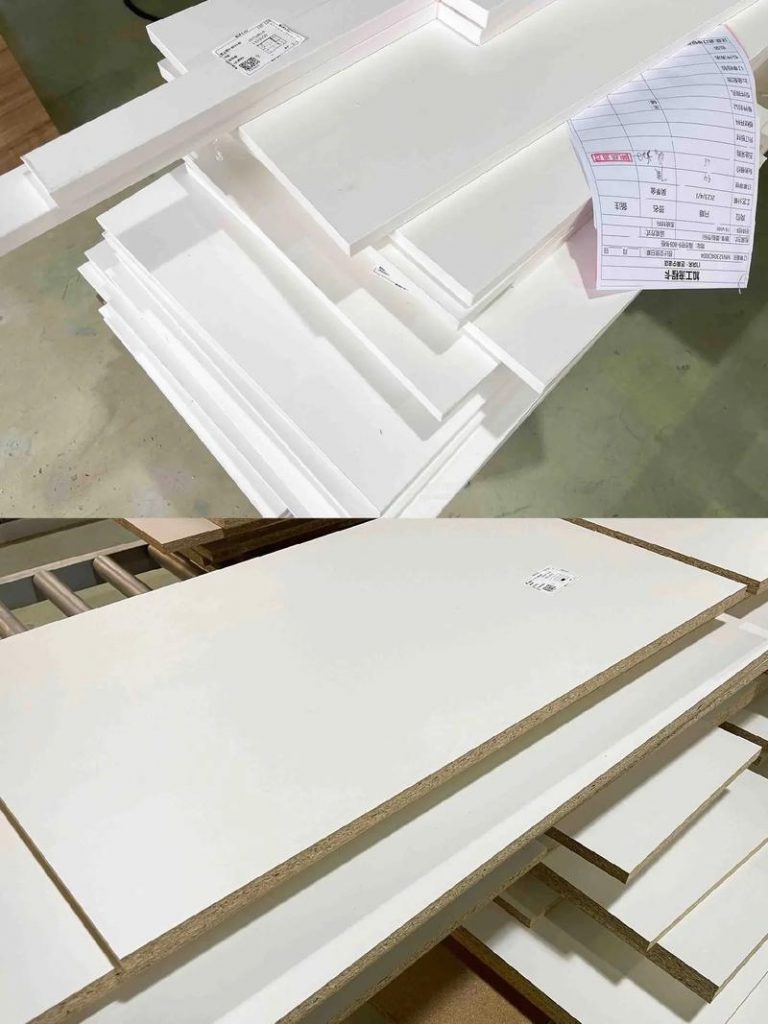
The Solution: Precise Size Measurement Machine
Intelligent custom furniture packaging line may include a size measurement machine to detect the size of the package and send size data to the carton machine. So that the carton machine custom-cut the corrugated boxes according to the exact dimensions of each order. The way of measurement includes:
• Physical measurement
• Light curtain measurement
Many factories would choose a line with size measurement machine to ensure the perfect size of the package box. In this way, they can not only have the standard cartons, but also save a lot of material cost.
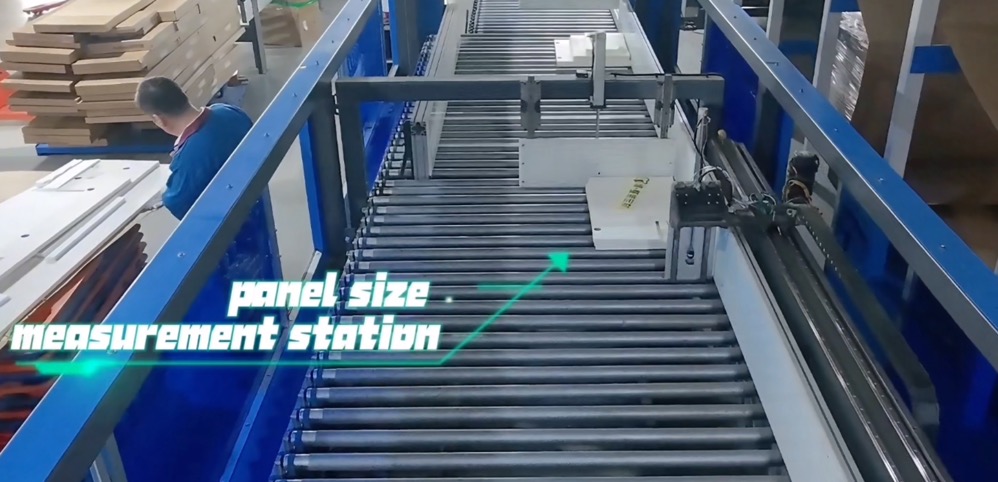
2. High Material Waste and Excess Inventory
The Challenge
Traditional packaging requires stocking multiple carton sizes, which leads to:
• High inventory costs
• Overstocking of unused boxes
• Excess material waste from trimming oversized cartons
The Solution: On-Demand Box Making Machines
Intelligent carton packaging machines custom-cut corrugated boxes according to the exact dimensions of each order. This ensures:
• Perfect-fit packaging, reducing wasted space
• Faster packing speeds with automated box creation
• Reduced material costs by eliminating oversized cartons
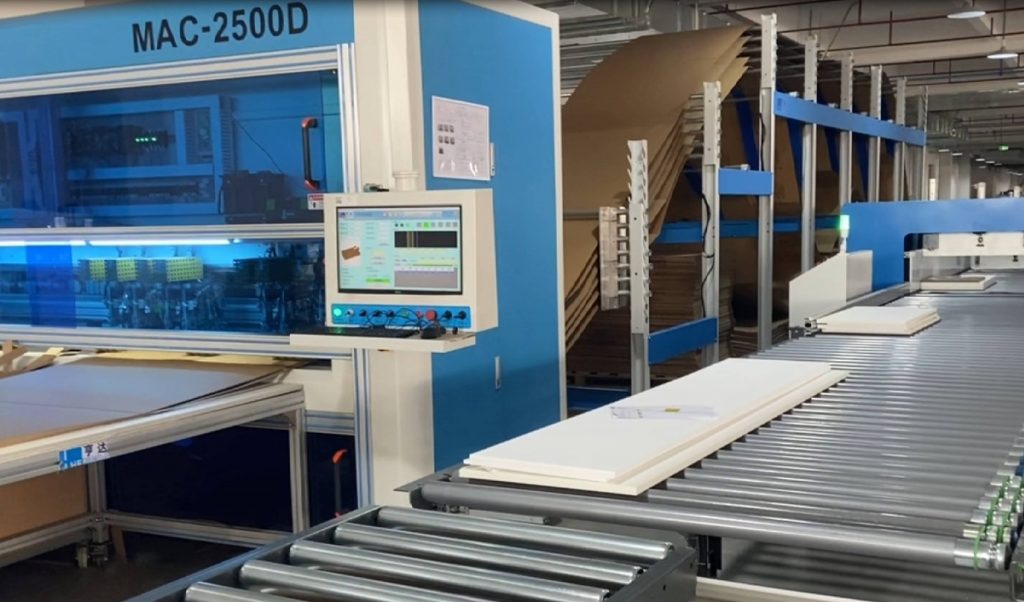
For example, a listed company in China manufacturing modular furniture using the box making machine and saved almost $55,000 of cardboard cost last year. By adjusting the programme of the carton machine, the cardboard usage rate reached the highest level, nearly no waste for the paper.
3. Labor-Intensive and Time-Consuming Packaging Processes
The Challenge
Many manufacturers still rely on manual packaging, leading to:
• Slow production speeds due to hand-cutting and box sealing
• Higher labor costs for packaging staff
• Increased chances of human error
• Untidy and low end appearance of the package
The Solution: Seamless Automatic Packaging Solution
We provide more than 20 kinds of packaging solutions for modular cabinet factory according to the factory layout, production volume, desire effect and many other factors to determine. Many factories that switched to automated packaging lines cut a lot of labor costs while increasing daily output.
By integrating automated packaging line, companies can:
• Speed up packaging by about 60%
• Reduce labor dependency and costs
• Ensure consistent and professional packaging quality
4. Product Damage During Transportation
The Challenge
Modular cabinets are made from delicate materials like MDF, plywood, or laminated boards, which are highly susceptible to:
• Scratches and dents
• Moisture exposure
• Structural damage due to poor packaging
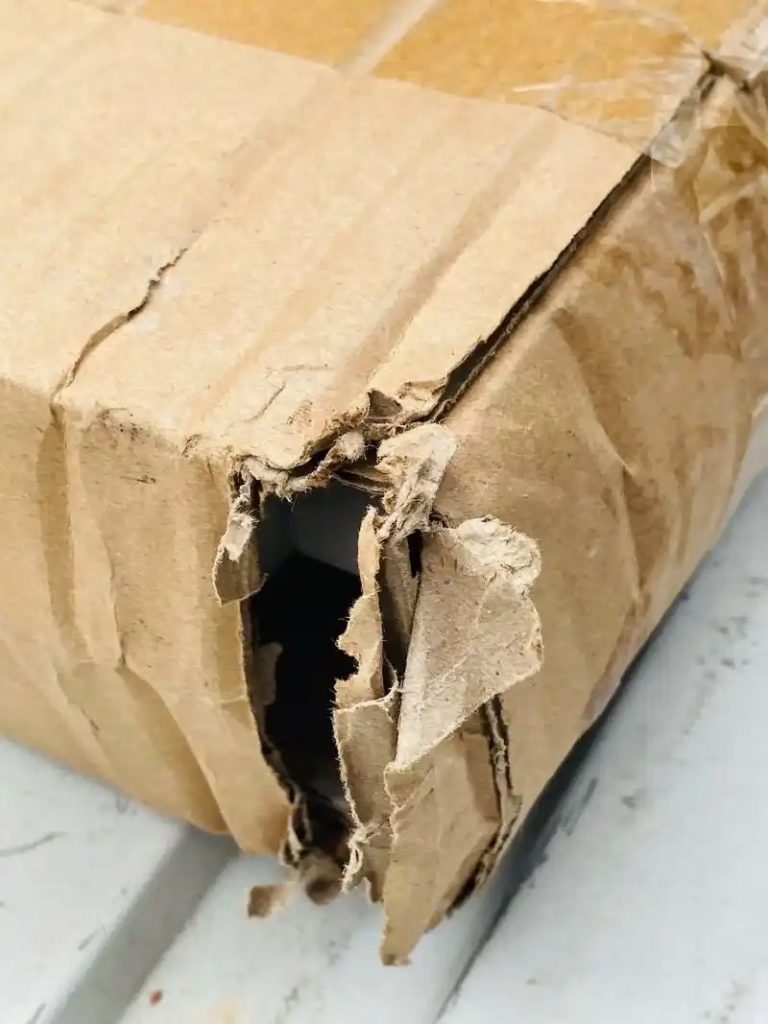
The Solution: Reinforced Corrugated Boxes & Delicate Box Sealing
Using reinforced corrugated boxes with precision fit, manufacturers can:
• Provide better product cushioning
• Reduce damage claims and returns
• Improve overall customer satisfaction
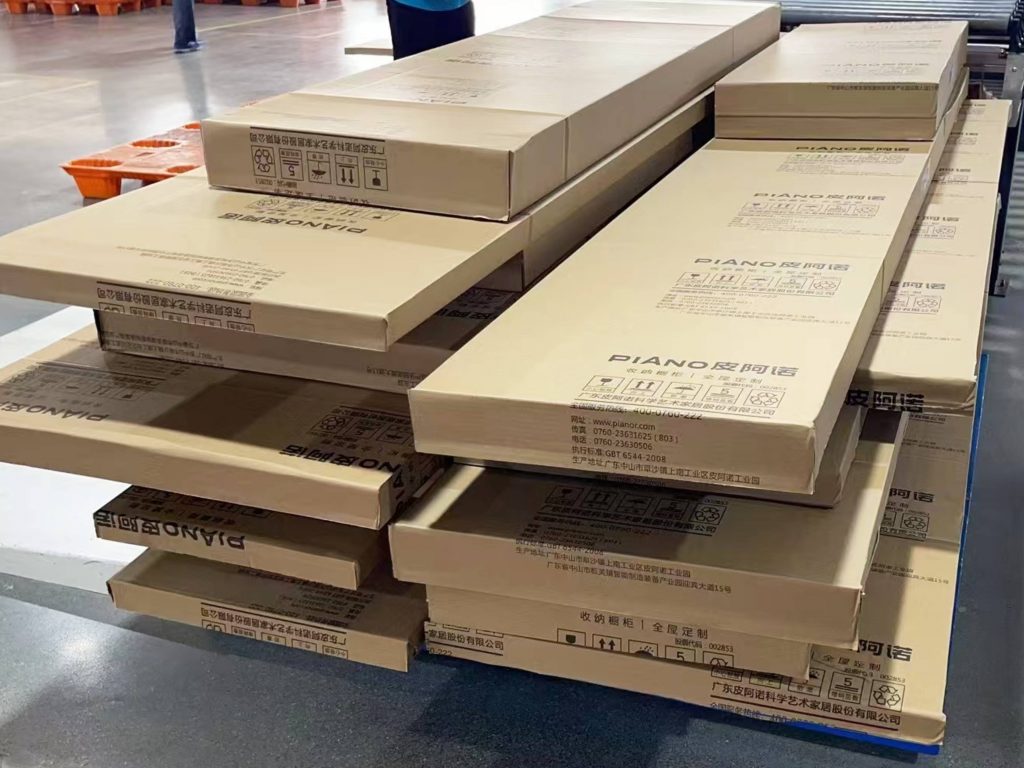
5. Increasing Demand for Sustainable Packaging
The Challenge
As environmental regulations tighten and customers become more eco-conscious, traditional packaging methods—such as using oversized cartons, unenviroment tape seal, and excessive materials—are no longer sustainable. Modular cabinet manufacturers face:
• Higher costs due to compliance with new environmental regulations
• Customer dissatisfaction with non-eco-friendly packaging
• Waste management challenges from excess packaging materials
The Solution: Eco-Friendly Box Sealing & Right-Sized Packaging
By adopting on-demand, right-sized packaging with fanfold corrugated cardboard, manufacturers can:
• Reduce material waste by up to 40%
• Cut down on sealing tape and non-recyclable materials
• Align with sustainability goals to meet customer and regulatory expectations
Like Ikea furniture, they have a very strict demand on eco-friendly packaging, using box sealing machine with EVA glue instead of sealing tape. And the have a very strict packaging appeareance standard as well to call on the environmental concept.
As the modular cabinet industry continues to grow, traditional packaging methods are no longer sustainable. Implementing intelligent packaging solutions can help manufacturers:
✔ Reduce packaging costs by up to 50%
✔ Improve product protection and customer satisfaction
✔ Streamline operations and boost efficiency
🚀 Want to revolutionize your packaging process? Contact us today to learn how our smart packaging solutions can transform your business!